solar energy
Strategy and actions for climate
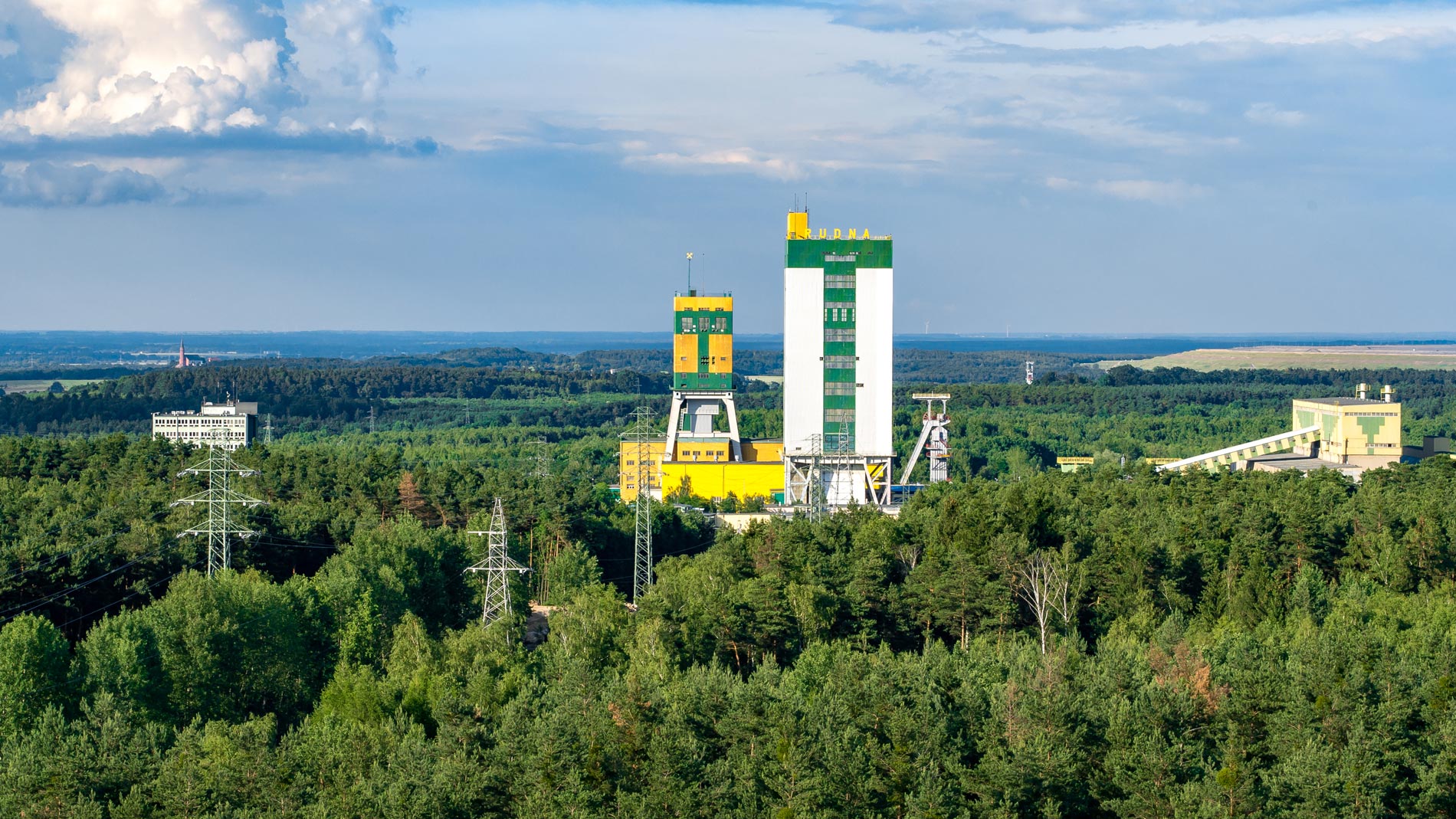
Use of raw materials being waste
KGHM Polska Miedź S.A. operations are consistent with the general rules of circular economy, such as: saving resources, minimizing waste production, using waste as raw materials for other processes in the company’s technologies and outside, low emissions or hermetic sealing of technological processes to reduce industrial burden for the environment. Examples of circular economy in KGHM Polska Miedź S.A. include production of road construction aggregate from copper slag. Slag is a waste (by-product) of the production process in smelters. Each year the Legnica Copper Smelter produces approx. 200 thousand tonnes and the Głogów Copper Smelter approx. 450-500 thousand tonnes of slag. Thanks to our knowledge and technology, this material is not dumped on a landfill site but it is given a second life. Owing to the technologies at the disposal of Group companies, the waste is converted into a full-value product used in road construction: high quality aggregate. In this way it is possible to manage the entire copper slag produced by the Company. Furthermore, the process of aggregate production based on the material supplied by the Company’s smelters also permits a reduction of emissions that would be released during the traditional process of aggregate creation. Over the past 10 years, KGHM Metraco, a Group subsidiary, has managed approx. 10 million tonnes of slag, which means that it was not necessary to obtain this amount of raw material from natural deposits, and at the same time such a huge waste volume was not dumped on landfill sites.
Every year the Company strives to introduce effective solutions to manifest its efforts to operate in line with the idea of circular economy. One of the components, which are excellent manifestations of circular economy, is production of road aggregates from copper slag. Slag is a waste (by-product) of the production process in smelters. Each year the Legnica Copper Smelter produces approx. 200 thousand tonnes and the Głogów Copper Smelter approx. 450-500 thousand tonnes of slag. Thanks to our knowledge and technology, this material is not dumped on a landfill site but it is given a second life. Owing to the technologies at the disposal of Group companies, the waste is converted into a full-value product used in road construction: high quality aggregate. In this way it is possible to manage the entire copper slag produced by the Company. Furthermore, the process of aggregate production based on the material supplied by the Company’s smelters also permits a reduction of emissions that would be released during the traditional process of aggregate creation. Over the past 10 years, KGHM Metraco, a Group subsidiary, has managed approx. 10 million tonnes of slag, which means that it was not necessary to obtain this amount of raw material from natural deposits, and at the same time such a huge waste volume was not dumped on landfill sites.
Aggregate produced by the Group were used for the execution of such projects as the construction of S3, S5, S6 or S11 express road, which is in progress at present. Material coming from smelters after an appropriate production process was used also for the expansion of the southern quarter of the Żelazny Most Tailings Storage Facility. Considerable quantities of the material are used also by local consumers that execute infrastructure projects commissioned by local authorities. The primary consumers are the largest construction companies specializing in road construction.
Scrap management
A high-quality copper scrap processing plant was installed within the core production line of the Legnica Copper Smelter and Refinery, which is the first stage for the Hybrid Smelter being designed in Legnica. Ultimately, it will be supplemented with the Scrap Trading Base, where the feedstock will be prepared for a dedicated installation for the remelting of the remaining copper-bearing materials coming from recycling.
As part of the first stage of the Hybrid Smelter in Legnica, the copper scrap processing technology with the use of a Revolving Casting-Refining (RCR) furnace was applied. The applied RCR furnace permits remelting copper scrap with the average 89% Cu content with the efficiency of at least 90 thousand tonnes of anode copper per year. The total production of anode copper at the Legnica Copper Smelter and Refinery in 2020 was 167.6 thousand tonnes, including 58.8 thousand tonnes produced by the RCR furnace. In 2020, in total 91 thousand tonnes of scrap were processed by the Legnica Copper Smelter and Refinery, which were thus returned to use in line with the circular economy concept.
Electromobility and low-carbon mining machines
One of the primary infrastructure-related obstacles in the development of electromobility is currently the deficit of fast charging points, whose range should cover the road network in Poland and whole Europe. The rapid development of transport based on electricity will pose an enormous challenge for electricity producers and distributors but will also give them an even 20% increase in the market of consumers. Bearing the above aspects in mind, KGHM Polska Miedź S.A. commenced decisive actions towards broadly understood electromobility in 2018. Through the gradual and consistent replacement of own transport fleet with zero-emissions electric vehicles, but above all through the development of ultra-fast charging stations available to the public in the LGOM area. The first station was created at the KGHM Head Office already in December 2018 and it was followed in 2019 by successive ones at the Głogów Copper Smelter, Legnica Copper Smelter and Lubin Mine Divisions. Each “charger” has three types of connectors, which ensures full compatibility with the vehicles that are available on the market. The stations are included in the IT system of Tauron Dystrybucja Serwis. The support for the electromobility development program provides for free charging for the users, which is beneficial to the environment and climate.
In addition, as part of actions for protection of the environment and climate as well as health and working comfort of the employees, the Company performs works aimed to reduce gas emissions from mining machine engines, in particular of nitrogen oxide and particulate matter. The objective is to reduce employees’ exposure to nitrogen oxide at workplaces and to achieve concentrations below 2.5 mg/m³ and to reduce the exposure to carcinogens to the level of 0.05 mg/m³ in terms of elemental carbon.
At present, the Company pursues an investment process related to the purchase of machinery, as part of which engines according to the Stage IV and V are gradually introduced, which enables several-fold reduction of emissions. Currently out of the 1,261 machines used in the Company, approx. 10% are low-emission machines. All new machines are purchased complete with engines complying with strictest flue gas purity standards. Replacement of all the machinery will be possible by the end of 2026.
The Company cooperates also with external manufacturers to test the functionality and effectiveness of mining machines with a battery electric drive. The effects of these measures include tests of a battery anchoring car at the Lubin Mine. A drilling car and a self-propelled electric transport vehicle will be delivered for testing in Q2 2021. Moreover, arrangements concerning commencement of testing of an electric charger at the Rudna Mine are at an advanced stage.
Energy from
own sources and RES
In 2020, the first photovoltaic power plant in Poland using the 4.0 technology was launched. This is an element of implementation of KGHM’s strategy aiming to increase the energy self-sufficiency and the use of Renewable Energy Sources.
KGHM’s ZANAM photovoltaic power plant is the first in Poland fully computerised and automated power plant using the 4.0 technology. The facility is equipped with a virtual Control Room and a modern High Resolution Monitoring System which supports full, precise, 24/7 diagnostics of the technical condition. The monitoring system works on the level of individual panels and not on level of strings, as before. This supports very precise identification of failures, if any, and reduction of maintenance trips and, consequently, reduction of maintenance costs. Annual energy production will amount to approx. 3 GWh. The power plant was built in accordance with the directions of development of photovoltaic power sector recommended by the International Energy Agency. This is a contribution to implementation of the low-emission energy management policy at KGHM and a tangible source of energy for our plant in Legnica.
The solutions applied in the photovoltaic power plant offer numerous possibilities, among others the possibility of configuration of automatic alerts. This shortens the failure response time. The monitoring of the technical condition of the photovoltaic panels and inverters uses advanced analytical algorithms based on the processing of Big Data, Machine Learning and Artificial Intelligence.
KGHM ZANAM Photovoltaic Power Plant in numbers:
energy source
location
KGHM ZANAM division in Legnica
In 2020 the Company reached a record electricity production level from Combined Cycle Units. The units generated in total over 0.5 TWh of energy, i.e. almost 16% of the Company’s total electricity demand. This significant share of cheap and ecological (compared to the burning of coal) energy from the units in the KGHM portfolio will allow the Company to both generate environmentally friendly energy and achieve savings of several dozen million PLN. The energy is used by: the Rudna Mine Division, Polkowice-Sieroszowice Mine Division and Głogów Copper Smelter Division. Electricity in Combined Cycle Units is generated by 4 Titan 130 Gas Turbines, with the capacity of 14.7 MWe, and 2 Siemens Steam Turbines, each with the capacity of 12.3 MWe.
The Group also has other in-house energy sources, which together with the Combined Cycle Units mentioned above covered 22.42% of KGHM’s total energy consumption in 2020 (nearly 1.5% more than in 2019). The figure below presents a breakdown of energy from own sources in 2020.
In 2020, KGHM Polska Miedź S.A. also took a range of actions to develop renewable energy sources:
- Applications for modifications in the urban design documentation have been submitted in order to commission photovoltaic units of the capacity of over 100 kW, located on land owned by KGHM Polska Miedź S.A. in:
- Lubin Municipality, of installed capacity of about 20MW.
- Warta Bolesławiecka Municipality, of installed capacity of over 50 MW.
- A pilot concurrent operation of two gas turbines in a combined cycle (gas and steam) unit in Głogów was conducted, generating 16 GWh of electricity more than in the originally planned generation schedule, which contributed to:
- Lower electricity production costs by about PLN 1.8 million.
- Lower CO2 emissions by over 4 thousand tonnes.
- KGHM ZANAM S.A, a subsidiary of KGHM, commissioned a photovoltaic plant of the capacity of 3.1 MWp.
Reduction of emissions from smelters and refineries
In order to minimize the negative environmental impact of metallurgical technologies and maintain fully operational equipment protecting the environment, the Company has successfully implemented adaptation of the units to the BAT Conclusions for the non-ferrous metals industry, including limitation of arsenic emissions. The parameters achieved thanks to a number of investment projects are much higher than the levels required by the law. The table below presents detailed results achieved by the completed investment projects in this area.
Results of investment projects in the area of unit adaptation to meet BAT Conclusions for the non-ferrous metals industry
Name of task/initiative | Expected adaptation to BAT Emission levels under BAT (BAT-AEL) | Task completion date Parameters achieved (in guaranteed parameter tests) |
---|---|---|
Modernisation of the PSz.1 bag filter dedusting system and Psz.2 and PSz.3 cartridge filters in Shaft Furnaces | BAT 39: | December 2019 |
Dust – 2-5 (mg/Nm3) | Dust – below 1 (mg/Nm3), | |
As – 0,05 (mg/Nm3) | As – below 0.05 (mg/Nm3), average 0.02 (mg/Nm3) | |
Construction of 2nd-degree wet dedusting system on the dryer dedusting units to reduce As and Hg emissions down to the BAT Conclusion levels | BAT 38: | December 2020 |
Dust – 3–5 (mg/Nm3) | Dust – poniżej 1 (mg/Nm3), | |
As – 0,05 (mg/Nm3) | As – below 0.02 (mg/Nm3), average 0.01 (mg/Nm3) | |
BAT 11: | Hg – below 0.004 (mg/Nm3), average 0.002 (mg/Nm3) | |
Hg – 0.01 – 0.05 (mg/Nm3) | ||
Design and construction of installation to eliminate arsenic from gases above TM-16 casting machines | BAT 44: | December 2020 |
Dust – below 15 (mg/Nm3) | Dust – below 2 (mg/Nm3), average 1.6 (mg/Nm3) | |
P-1 Air-tight sealing of conveyor belt pulling stations for carrying copper concentrate and bedding and blending store | BAT 8 i BAT 25: | October 2019 |
Specify the required adaptation method to prevent diffuse emissions from pre-treatment of raw materials, primary and secondary materials and their transport, or to reduce the emissions. | Sealed conveyor systems were applied for transport and handling of dust generating concentrates, as well as fluxes and fine materials; mounting of roofs over conveyors for handling non-dust emitting solids (compliance with BAT8a, BAT8b, BAT25). | |
PG Installation feeding de-leaded slag into flash furnace | BAT54: | December 2020 |
Specifies methods to reduce the amount of copper production primary and secondary waste materials to be stored. | The installation enables air-sealed transport of the waste material, i.e. de-leaded slag, to flash furnace for metal recovery (compliance with BAT54). | |
BAT90: | A pneumatic transport system applied for dust-generating materials (compliance with BAT90a). | |
Specifies the required adaptation method to prevent diffuse emissions from pre-treatment of raw materials, primary and secondary materials or to reduce the emissions (for lead production). |
In addition, the graphics from the investor presentation to be shown:
161 mn PLN
Program to adapt the technological installations to BAT
Conclusions
Construction and start-up of the following completed:
- HM Głogów
- an installation for the transport of de-leaded slag for processing in the flash furnace,
- bypass gases pipelines from the flash furnaces to the sulphuric acid plant,
- a warehouse and storage area for lead-bearing materials to eliminate fugitive dust emissions
- HM Legnica
- an installation to eliminate arsenic-bearing dusts from concentrate drier gases and from above the anode casting machine